Cement production equipment
2500 tons of new dry cement machinery of
complete sets of equipment
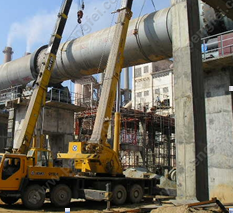
The
main process flow and host configuration
1)
limestone crushing, conveying and
storage. Limestone is broken by a MB56 /
75 crusher ( outdoor arrangement ) were
broken. When the feeding ore maximum
size is smaller than 1500mm, the
particle size is smaller than 75mm, the
crushing capacity of 500 ~ 600t / h; out
of the limestone crusher by belt
conveyor to a 80m circular limestone
prehomogenizing storage yard ( reserve
34100 T ) for advance homogenization and
storage, stacker ( heap material: 800t /
h ), ring cantilever continuous cloth,
reclaimer ( reclaiming capacity: 500t /
h ) bridge, end, center of discharging
material. After all of the limestone by
belt conveyor to raw material
proportioning station.
2)
auxiliary raw material storage, crushing
and transportation. Auxiliary materials
sand, iron ore from motor transport into
the factory, unloading to the open yard
storage. Among them, the sandstone open
yard specifications for the 60 m x 20m,
reserve 5100 T; iron ore open yard 32 m
x 20m, reserve 2730 t. Sand, iron ore
and a PC1609 hammer crusher, when the
feed particle size is smaller than
600mm, the particle size is less than or
equal to 25mm breaking capacity of 50 ~
70t / h; the broken sandstone, iron ore
by the belt conveyor to raw material
mixing station ingredients stored in
respective library. Auxiliary raw fly
ash by bulk vehicle into the factory, by
dumping system via pipeline into raw
material proportioning station fly-ash
base storage.
3) raw
material proportioning station. Raw
material batching station with
limestone, sandstone, iron ore, coal ash
four ingredients Library (
specifications are 12 m ID, 25m,
220016002200770t reserves respectively
), bottom are respectively provided with
a weighing feeder, by setting the
mixture ratio of the material is
calculated. With raw materials from the
conveyor belt into the vertical grinding
system for grinding.
4) raw
material powder and waste gas treatment.
Raw material grinding mill using MLS3626
( outdoor arrangement ), the drying heat
source for a preheater waste gas. When
the grinding particle size of raw
materials 90% 75mm, product fineness of
80 u m square hole screen more than <
12%, into the grinding material water <
8%, < 1% of raw meal moisture,
production system for 185t / h ( wear ).
Raw meal by fine powder separator with
humidifying tower and electric dust
collector to collect the dust mixed, via
a chute, bucket elevator to the raw meal
homogenizing silo for homogenizing and
storage; the grinding waste gas through
the electric dust collector purification
treatment, is discharged into
atmosphere.
5) raw
meal homogenizing silo and kiln feeding.
A qualified raw material by grinding the
garage top raw material distributor
multiple points of entry into a 18m x
50m CP ( effective reserves of 9000t )
of raw meal homogenizing silo
homogenizing, through the discharging
device quantitative unloaded into the
kiln feeding system. Kiln feeding system
is provided with a loading bin, bin has
a metering and flow control device,
after the measurement of raw material
from bucket type lifting machine feeding
into kiln preheater system.
6) the
clinker burning system and storage.
Clinker burning system consists of low
loss single series of online type five
stage preheater and calciner ( RF5 /
2500 type, into the kiln decomposing
rate of greater than 90% ), a 4 x 60m,
LBT32216 new control flow grate cooler,
are NCDRI technology. Among them : 1,
kiln clinker with grate cooler cooling
by chain bucket conveyor, into the 2
conveyer for 18 x 40m round Library (
effective reserves 2-10000t ) storage,
warehousing clinker with unloading
device, belt conveyor to cement clinker
and cement batching station outside; 2,
the hot end of the high temperature gas
cooled machine part through the three
duct into the decomposing furnace as
decomposition furnace burning gas, The
temperature of the heat into the coal
mill as raw coal drying heat source; the
tail end of the exhaust gas by electric
dust collector purification before being
emitted into the atmosphere, exhaust gas
dust concentration ( converted into
standard conditions ) is less than 100mg
/ m3.
7) coal
storage and transportation, coal powder
preparation and delivery. Motor
transport into the plant after the coal
using 21m x 113m hanging garage
(reserves 9300t ) storage and
homogenizing. The garage is provided
with two bunker, one is considering
shortening the crane walking distance,
on the other hand, is to consider the
different quality of two kinds of coal
collocation, bin bottom is provided with
a weighing feeder, the measurement by
the belt conveyor coal to the coal mill
to grind. Coal powder preparation using
a MPF1713 roller mill, outdoor
arrangement, when ground water is less
than or equal to 10%, coal moisture less
than 1%; coal particle size is smaller
than 50mm, pulverized coal fineness 80 u
m square hole screen more than 11%,
yield of 20t / h system. The mill
pulverized coal with gas enters the
separator separation, finished
pulverized coal by the airflow into the
air box pulse bag type dust collector
collected by screw conveyor into two
pulverized coal storage, waste gas after
purifying the atmosphere. Pulverized
coal bin is arranged at the bottom of
coal powder measurement system, the
measurement system of pulverized coal
measures are fed into the kiln head and
decomposition furnace combustion.
8) slag
drying and conveying, gypsum crushing
and transportation. As the admixture of
slag by car into the plant discharged
into the open yard for storage, forklift
slag into the bucket, the bucket
elevator into the phi 2.4 x 18.350m
dryer for drying, the drying capacity is
greater than or equal to 30t / h ( the
initial material moisture 20%, final
1.5% water ). Gypsum by motor transport
into the factory, unloading to reserve
4000t open yard storage, after heavy
slab feeder feeding PFC-1609 hammer
crusher (when the feed particle size is
smaller than 600mm, the particle size is
less than or equal to 25mm production
capacity of 50 ~ 70t / h) is broken, the
broken gypsum by bucket machine, belt
conveyor to gypsum bin storage.
9) the
cement grinding, transportation and
storage. Cement batching station with
gypsum, limestone and clinker, slag four
ingredients for clinker silo, which is
10 m ID, 22m, 2000t reserves; gypsum
slag pool library, and limestone are 8 m
ID, 22m, reserves are 800, 400 and 900t.
The reservoir bottom are respectively
provided with a weighing feeder, by
setting the mixture ratio of the
material is calculated. Grog ingredient
reservoir side a clinker bulk
facilities, out for clinker. Four kinds
of material in the feeding metering
equipment according to the proportion of
unloading, by belt conveyor to two sets
by 3.8 dia x 13m mill with high Xiaoxuan
powder machine consisting of a circular
flow of cement grinding system for
grinding, when the cement specific
surface area is 3200 ~ 3400cm2 / g, a
single set of production system for 75t
/ h; the abrasive material from the
bucket into the high Xiaoxuan powder
machine for sorting, coarse powder mill
back to grinding, cement products by air
box pulse bag type dust collector
collected by air conveying chute, bucket
elevator to 8 15 m ID, 34m cement base (
single storage for 5300t ) in storage.
Cement grinding system for exhaust gas
into the efficient air box pulse bag
type collector is drained to the
atmosphere after purification. Outbound
cement consists of bottom unloading
device after discharged, by a belt
conveyor, bucket elevator, air conveying
chute into the cement packaging workshop
and bulk cement silo. The cement
packaging uses two eight mouth rotary
packing machine, packaging machine each
ability for 90t / h, packaging bags of
cement, the bag unloading conveyor
system into 84m x 30m bagged cement
products store inside the library (
reserves of 6000t ), also can be
directly shipped loading. Bulk cement
storehouse with two facilities for bulk
cement trucks, bulk of car use.
The
technical level and the main technical
characteristics
(1)
creative general layout. This project
covers an area of limestone mine to
close near the steep mountain slopes,
not to occupy farmland, overall planning
to meet the process smooth and
reasonable at the same time, the
original combination of fuel and cement
products import factory direction, and
taking into account the site topography
feature and external traffic conditions,
from west to East is sequentially
provided raw fuel storage area, the main
production line, planning to set aside
the two phase of the production line,
the front area, the district are
arranged in parallel, functional
partition is clear; and the height
differential bench set District,
beautiful visual effect. Another
consideration of limestone mine is
located in the west side of the higher
terrain of the site, according to the
characteristics and the combination of
process flow, raw fuel storage area is
arranged in the western higher
locations, both to reduce the field
leveling earthwork engineering quantity,
but also shorten the belt conveying
distance, improve land utilization rate,
reduce the overall project investment
cost. In addition, in order to avoid the
middle of a flood ditch, overall
planning, clinker production line and
the cement grinding system are arranged
on the sides of the trench to flood,
belt machine for material
transportation, which can meet the
requirements of the process, and
reasonable use of the terrain, avoiding
flood ditch for the entire production
line effect.
(2)
selection of equipment in fully reflect
the domestic and advanced and reliable,
energy efficient. For example: 1
adopting a set of vertical mill as raw
material grinding system, and compared
with traditional ball mill system, the
grinding efficiency is high, the drying
capacity, low power consumption,
investment and other significant
advantages, in which only the power
consumption with a ball mill system can
achieve the unit yield compared to
saving 4 ~ 6kWh / T, annual savings
4760000 - 7130000 kWh. To adopt vertical
mill to replace the traditional air
swept mill pulverized coal preparation
system, the power consumption can be
saved about 30%. The raw meal
homogenizing silo with continuous
homogenizing silo, the unit of raw meal
consumption is 0.3kWh / T, intermittent
mixing raw material of less than 0.4kWh
/ T. The kiln end with online type
decomposition furnace of five stage
cyclone preheater kiln feeding system,
when the temperature is high up to 900
DEG C, into the kiln decomposing rate
achieve 90% above, the clinker burning
heat energy consumption control in
3137kJ / kg ( 750kCal / kg ) the
following. The kiln head, in addition to
the selected kiln tail sealing device,
also adopted the new efficient three
channel coal burner tube, through
changing the air velocity and volume
ratio, flexible adjustment of the shape
of the flame and combustion intensity,
in order to adapt to the condition in
the kiln, thereby reducing the coal
consumption, increase the yield. Clinker
cooling using control flow reciprocating
grate cooler, high thermal efficiency,
energy saving and consumption reducing.
The selection of high dust collecting
equipment, pay attention to
environmental protection, the factory
discharges exhaust gas containing dust
concentrations were lower than the
national emission standard, which can
save a large amount of raw material,
fuel and power, saving energy, reducing
environmental pollution of. The large
fan, conveying equipment are selected in
low-pow devices ( such as air chute to
replace the screw conveyor ), reserve
coefficient does not exceed the
specified range. In addition to raw meal
in preheater, pulverized coal, lump, all
powdery materials are used to save the
energy of mechanical transmission.
The
production practice proved: this project
adopts the new dry process production
line system technology is mature and
reliable, design optimization, debug
successfully, general layout reasonable
and concise and beautiful. Current
annual run rate above 90%, the average
yield reached 2730t / D above; heat
consumption of clinker < 3136kJ / kg; a
cylinder preheater outlet temperature
less than 338 DEG C; resistance to
4590Pa; upon detection, all emission
point emission concentration of the dust
( converted into standard conditions ) <
70mg / m3, benefit apparent.
|